O Desafio:
Os rompedores hidráulicos (hammers) são equipamentos responsáveis por reduzir a granulometria do minério para que ele tenha o tamanho adequado à grade do circuito de britagem.
A Mina de Cuiabá, de propriedade da AngloGold Ashanti, possui três hammers no subsolo, a 840 metros de profundidade, os quais eram operados por controle remoto há cerca de dez metros de distância. Esta operação local no subsolo é responsável por uma série de inconvenientes:
- Ambiente insalubre;
- Risco de acidentes provenientes de equipamentos móveis e desabamento de placas de rochas;
- Tempo de operação reduzido devido ao deslocamento do operador ao subsolo e espera das detonações que ocorrem a cada turno;
A figura a seguir exibe a operação local do hammer:
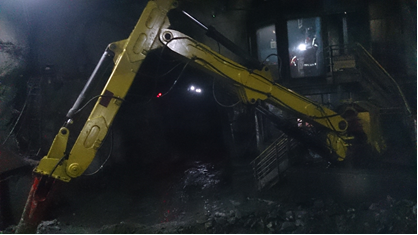
A solução:
A solução foi implementar a operação remota dos hammers a partir de uma sala de controle na superfície.
O projeto envolveu a implementação de uma rede de fibra ótica até a superfície, a instalação de câmeras e TVs, a instalação e programação de um PLC para cada hammer no subsolo com a função de receber os pontos de IO das unidades hidráulicas e dos sensores, a instalação e programação de um PLC na superfície com a função de receber os pontos de IO do posto de comando (cadeira de comando com dois joysticks), instalação e programação de duas IHMs no subsolo para supervisão dos hammers e instalação e programação do sistema de supervisão na sala de controle para sinalização, alarmes e operação dos hammers.
Os Resultados:
- Ganho de produtividade devido aos hammers poderem operar 24 horas por dia. Havia uma perda de 2 horas de operação por turno com deslocamento e espera por detonação;
- Redução na exposição e o tempo com transporte, pois os operadores permanecem na superfície;
- Posto de comando 100% ergonômico e confortável, o que favorece a qualidade da operação dos equipamentos;
- Possibilidade de operar os três hammers simultaneamente com um único operador;
- Aumento da segurança com eliminação da exposição do operador a equipamentos móveis e desabamento de placas de rochas.
As Tecnologias:
- PLC Rockwell CompactLogix 1769-L39ER;
- Sistema de Supervisão FactoryTalk Machine Editon v8;
- IHM PainelView 1000 (Sistema de Supervisão FactoryTalk Machine Edition v7).