O Desafio:
O processo de lingotamento e empilhamento de alumínio da área da Fundição da ALBRAS era controlado por diversos sistemas de automação e TI obsoletos, desenvolvidos em momentos diferentes, de difícil manutenção e com muitas tecnologias já ultrapassadas como Delphi 3.0, SQL Server 2000 e comunicações seriais.
Existiam três sistemas de supervisão independentes, além de outros sistemas de TI onde operadores efetuavam a entrada manual de dados relativos à produção. Este ambiente ocasionava alguns problemas de duplicidade de informações e funções como, por exemplo, a criação de fusões em mais de um sistema, transferência de informações entre os sistemas, dentre outras.
A figura a seguir ilustra a situação encontrada:
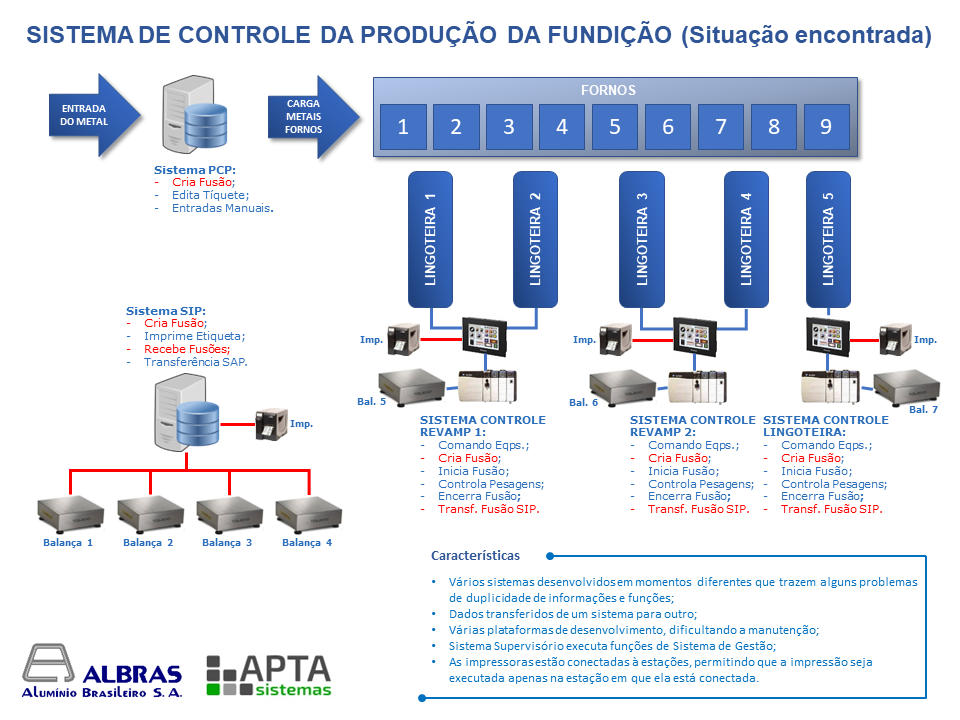
A Solução:
A solução para o sistema envolveu as disciplinas de TA e TI, ambas de grande domínio e experiência da APTA. Foi executada uma análise detalhada das regras de negócio para a separação clara das responsabilidades dos sistemas: o Sistema de Controle responsável pelo comando dos equipamentos e leitura de pesagens das pilhas e um sistema de TI responsável pelas funcionalidades de gestão.
Foi desenvolvido um sistema de TI responsável por todas as funcionalidades de gestão das fusões, tais como, cadastros, recebimento das pesagens de metal líquido vindo das reduções, leituras das pesagens das pilhas dos lingotes de alumínio dos PLCs (via OPC), leituras das análises químicas, envio dos dados de produção das fusões para o SAP, dentre outras.
O sistema de TI é composto de uma aplicação Web para as telas de interfaces, serviços para as atividades de background como leitura das pesagens e análises químicas e um aplicativo Windows Forms que roda nas IHMs das balanças para controle das pesagens.
As três aplicações do sistema supervisório foram unificadas em uma única aplicação com servidores redundantes, além da atualização tecnológica da plataforma. Todas as funcionalidades de gestão das fusões foram eliminadas e migradas para o sistema de TI.
Os programas dos PLC’s tiveram suas rotinas de pesagens de pilhas reescritas para que as pesagens sejam empilhadas em uma FIFO e o sistema de TI, a partir de uma comunicação OPC, desempilhe as pesagens e as gravem em seu banco de dados.
O objetivo da FIFO foi permitir uma contingência em caso de falha na rede, ou seja, como o PLC está conectado diretamente às balanças via rede de campo (Devicenet), a pesagem continua sendo executada e os pesos das pilhas são empilhados pelo PLC em sua FIFO para posterior leitura pelo sistema TI, assim que a rede seja reestabelecida.
A figura a seguir ilustra a solução implantada:
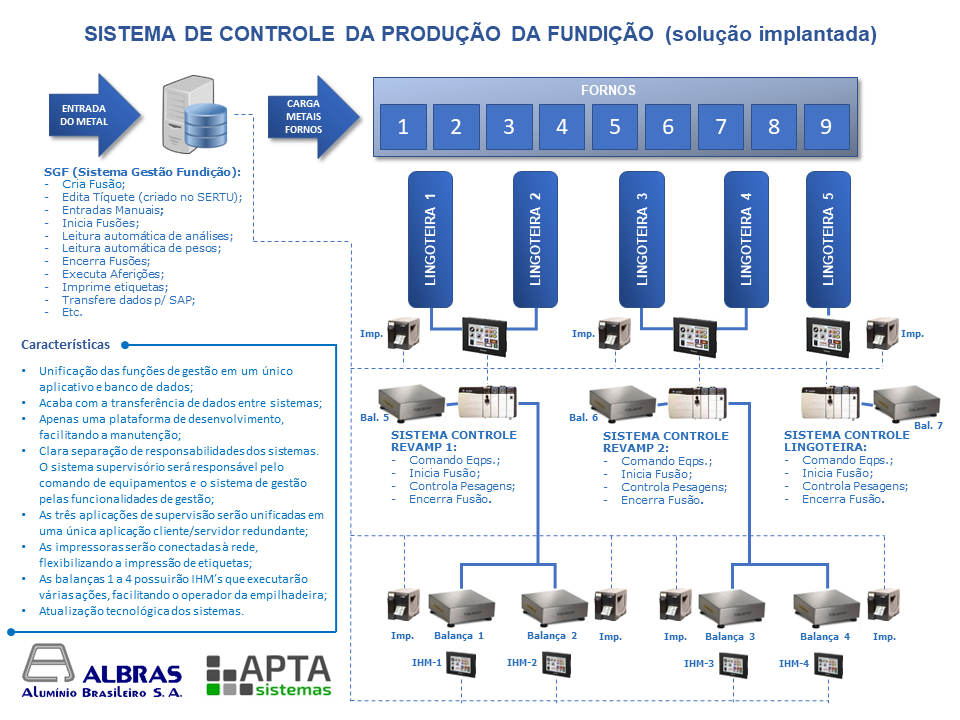
Os Resultados:
- Eliminação da duplicidade de informações evitando intervenções manuais para ajustes, trazendo mais confiabilidade ao sistema e eliminando erros no lançamento das produções no SAP;
- Maior disponibilidade do sistema, uma vez que a unificação dos sistemas proporcionou maior robustez e diminuição drástica das manutenções;
- Atualização tecnológica dos sistemas;
- Maior flexibilidade das pesagens das pilhas já que o novo sistema trouxe novas funcionalidades como transferência da pesagem para outra balança, evitando retrabalho e perda de tempo.
Em conclusão, o sistema CMS é fundamental para o sucesso da empresa na produção de fundição de alumínio. As novas funcionalidades permitiram um rastreamento em tempo real das pilhas de lingotes de uma fusão, pesos de sucatas e anteligas. Os relatórios são fundamentais para a tomada de decisão e aumento da eficiência do processo.
Além disso, as novas funcionalidades permitiram uma melhor gestão dos recursos e a otimização da produção, trazendo resultados positivos e aumento da competitividade da empresa.
As Tecnologias:
O sistema de TI foi baseado em modelo físico arquitetural de sistema distribuído em rede, e em modelo lógico arquitetural de n-camadas, seguindo as melhores práticas indicadas pelo conceito de Domain Driven Design e foi implementado com a utilização da seguinte plataforma tecnológica:
- Microsoft .NET – framework versão 4.8;
- Linguagem de programação C#;
- Microsoft ASP.NET MVC;
- Microsoft Windows Communication Foundation;
- Framework Spring.Net;
- Framework NHibernate;
- Framework Apta;
- Framework CSS Bootstrap;
- Componentes Javascript JQX Widgets;
- Banco de Dados Microsoft SQL Server.
O sistema de TA foi baseado nas seguintes tecnologias:
- Sistema supervisório iFix versão 5.9 com um par de servidores redundantes e quatro estações clientes;
- PLCs da família ControlLogix do fabricante Rockwell;
Rede de campo DeviceNet para comunicação com as balanças e com os acionamentos.
As imagens do sistema implantado:
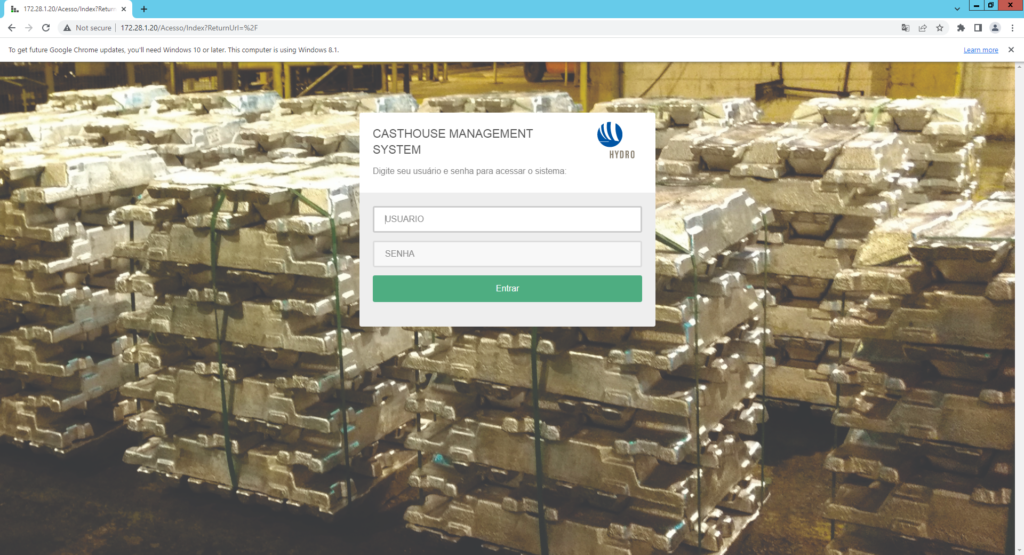
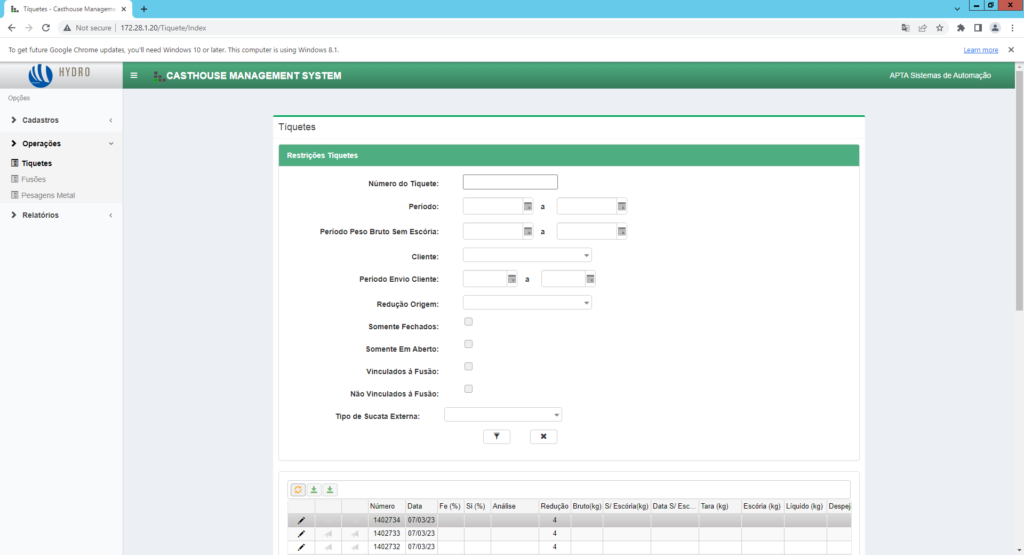
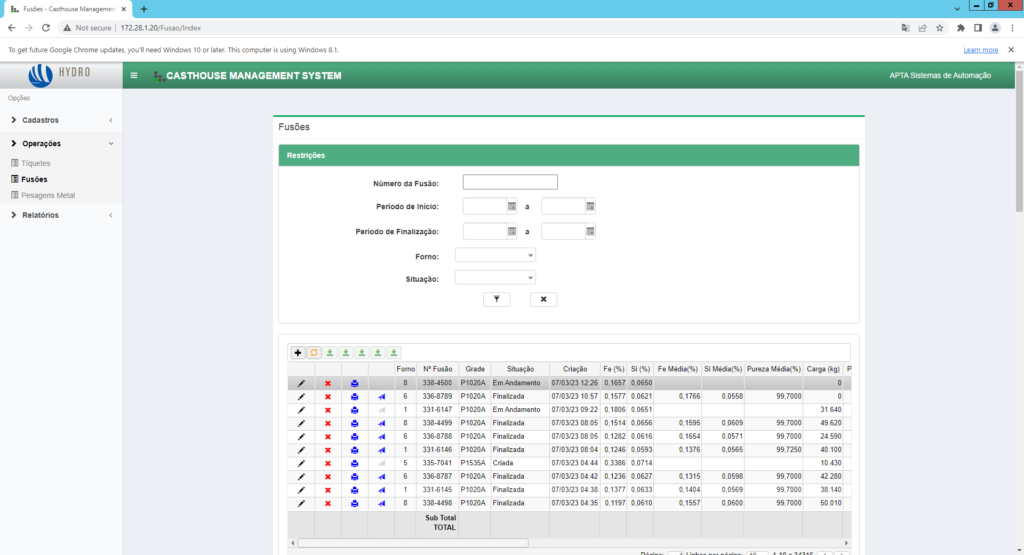